Figure No.1 Vibration signatures coupled to load data for fan and compressor RCA of surge events,resulting in motor failures, and foundation cracks.
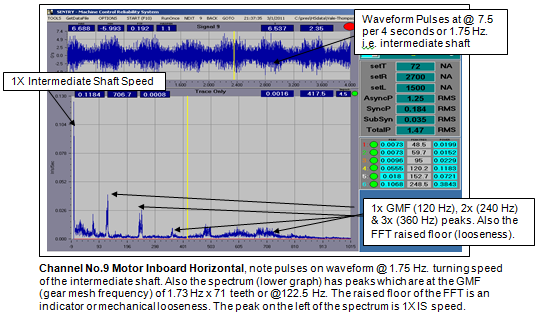
Figure No.2 Bearing & Gear Defect detection
Solution: Tighten anchor bolts & re-gout foundation sole plate & replace pinion gear.
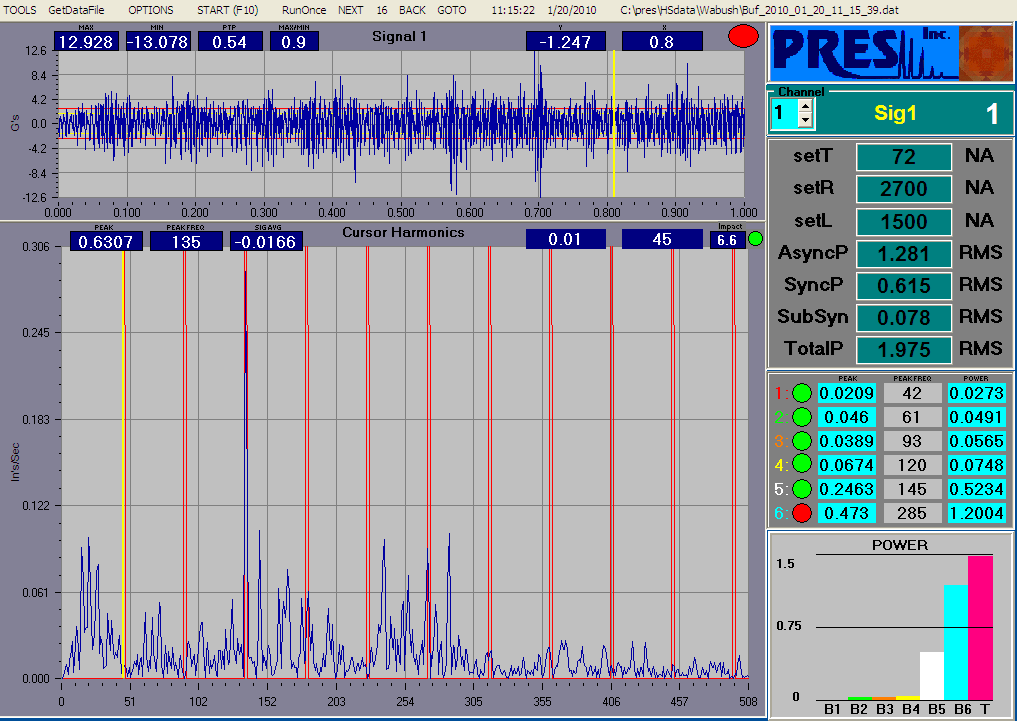
Figure No.3 Harmonic Analysis, Narrow Banding of the spectrum, waveform pulse analysis. Using vibration analysis the condition of bearings,
shafts, gearing, coupling can be determined with magnetically or stud mounted sensors.
Solution: Re-alignment of motor to gear box allowing for thermal growth.
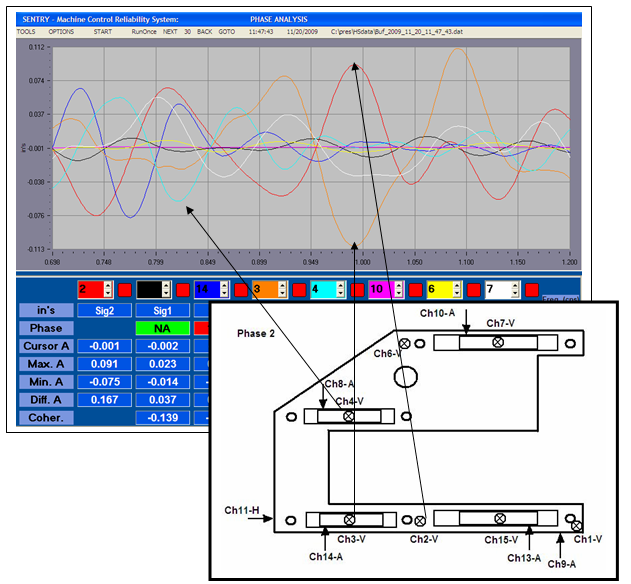
Figure No.4 Multi-Phase Analysis Sole Plate, Foundation, & Structural Steel Stability for RCA of bearing and gear failure. Phase provides direction of Vibrational force.
Solution: Steel stiffeners added to base structure f(n) shift
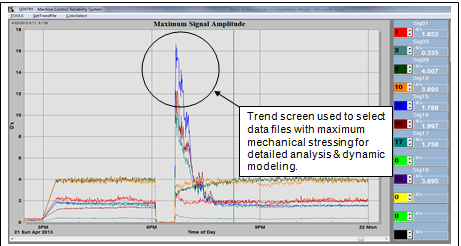
Figure No.5 Using Trending for selection of maximum load data when mechanical defects are most apparent.
Solution: Rolling Mill Chatter
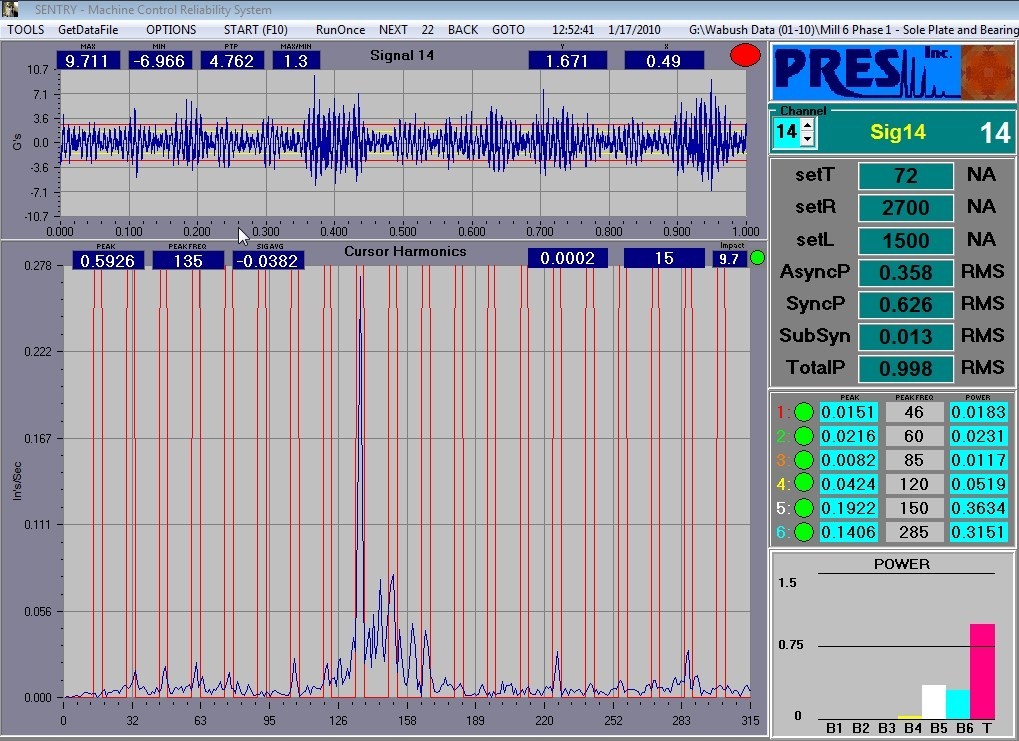
Figure No. 6 Sound & Acoustics with correlation to vibration signatures to determine root cause and solution.
Solution: Gear manufacturing defects excite “resonates” housing increasing noise level, gear quality improved.
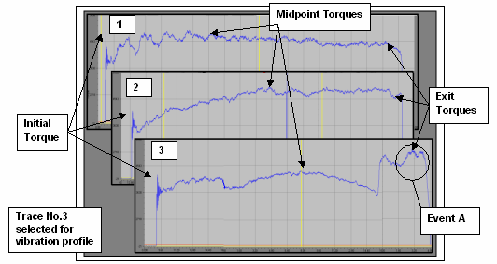
Figure No. 7 Torque & Strain measurements for variable loading. High torque amplification factors result in high stress for bearings, shafts. gears, & rolls.
Solution: Rolling mill computer model tuned to run higher yield steels.

Figure No.8 Natural Frequency Determination Modal Analysis when excited f(n) can become a very destructive force. Calculated F9n) can be confirmed via impact testing.
Solution: Gear f(n) shifted to avoid resonance from mill RPM
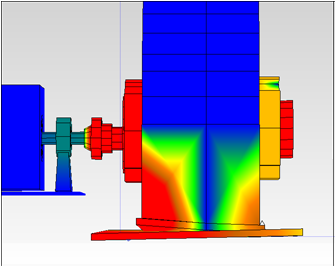
Figure No. 9 ODS (operational deflection shape) and dynamic analysis illustrating sole plate (base) instability and bearing stressing
Solution: Repair foundation & Sole Plate.
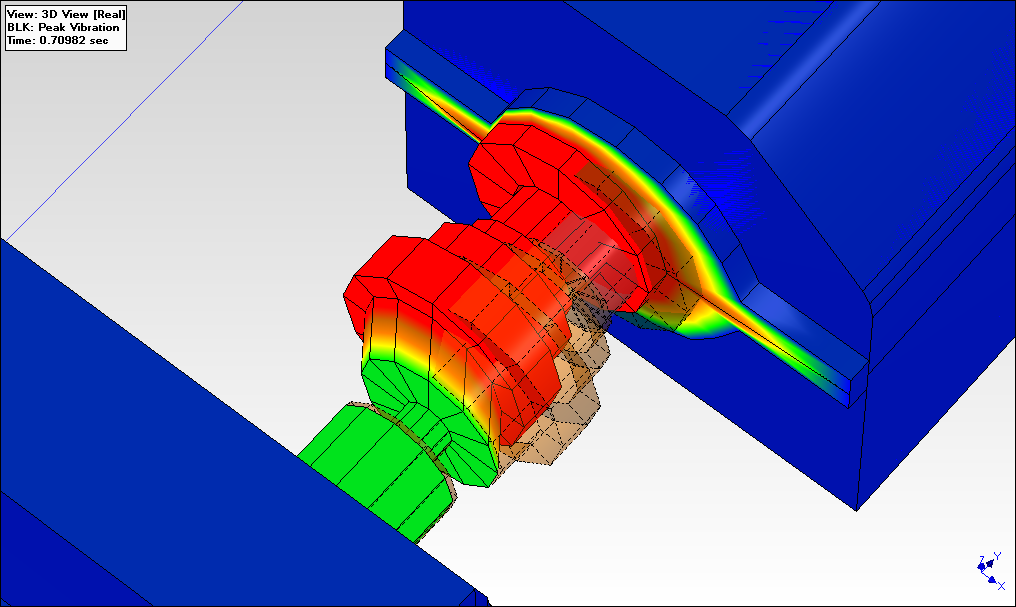
Figure No.10 ODS Model of coupling thrust instability during peak loading a transient event
Solution: Change Coupling model to high thrust model.
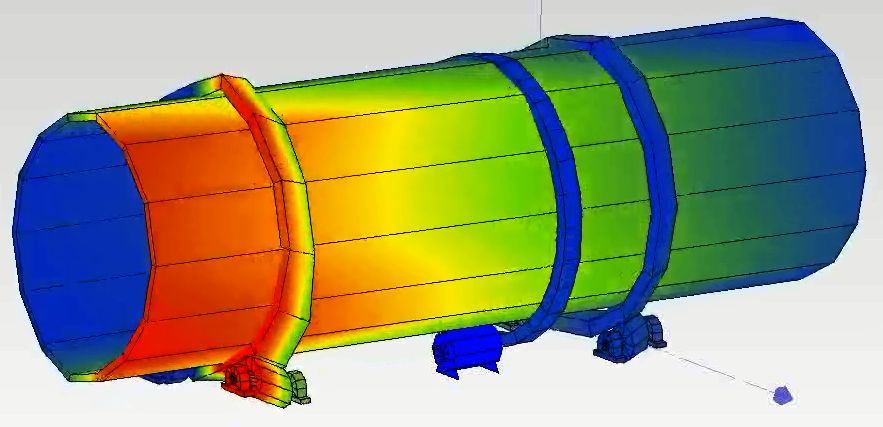
Figure No. 11 Reactor rotational analysis
Solution: Alignment of support rolls.
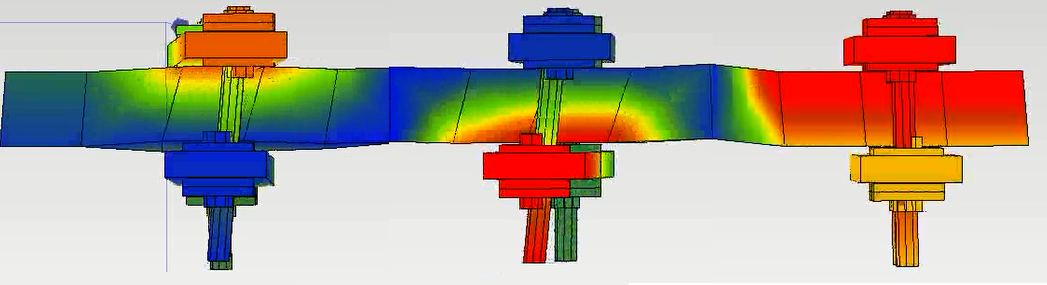
Figure No.12 Mill Stand & Steel Strip Instability Resulted in heavy impacts with mill stands
Solution:Stabilize strip with weld alignment, balance mill loads.
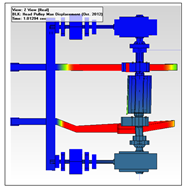
Figure No. 13 Conveyor Structural Dynamics
Solution: Add stiffeners to bearing structure Re-alignment of motors to share loading
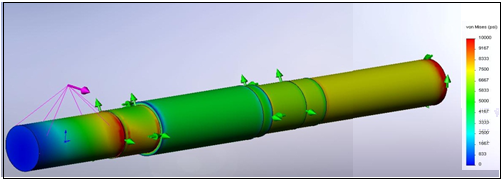
Figure No. 14 FEA of critical components
Solution: Change bevel to ring gear alignment Improve lubrication to gear mesh.
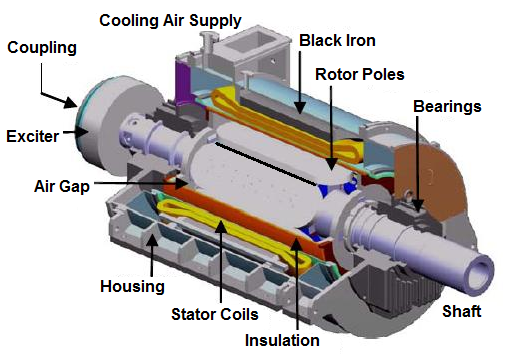
Figure No. 15 Analysis of specific motor elements
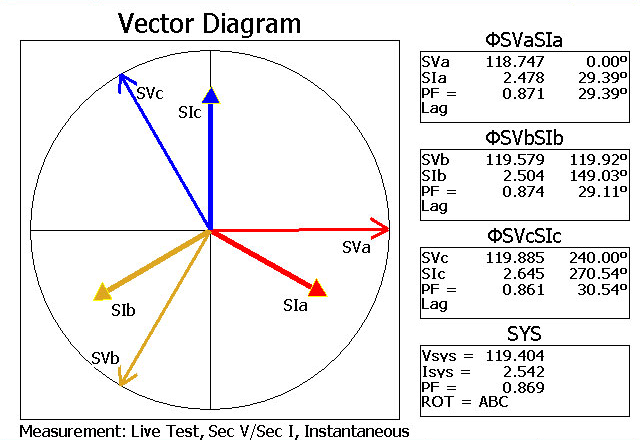
Figure No. 16 Electrical Vector Analysis for per phase electrical balance.
Solution:diagnose uneven air gap, insulation problems, excessive heating, loose connections, and poor quality electrical power.
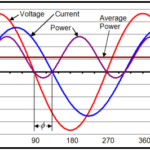
Figure No.17 Motor Efficiency & Power Stability using voltage and current waveform
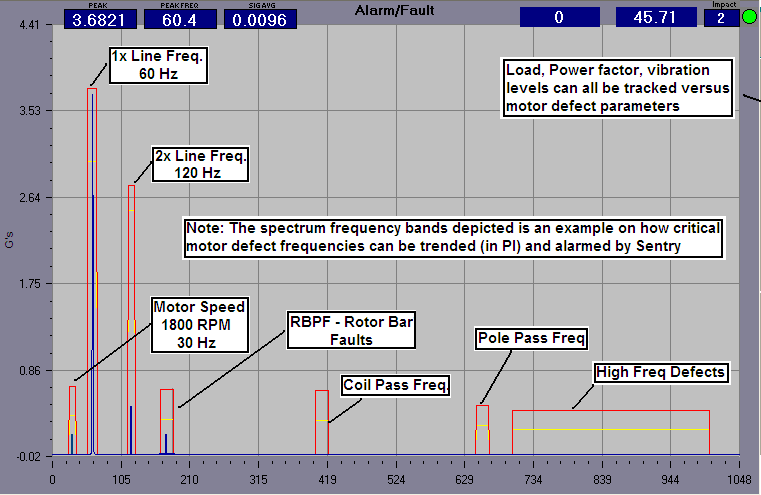
Figure No.18 Motor Spectrum Analysis
Solution: Rotor bar, & stator coil defects,can all be determined by vibration analysis electrical measurement are then used to quantify the problem and assess repairs.
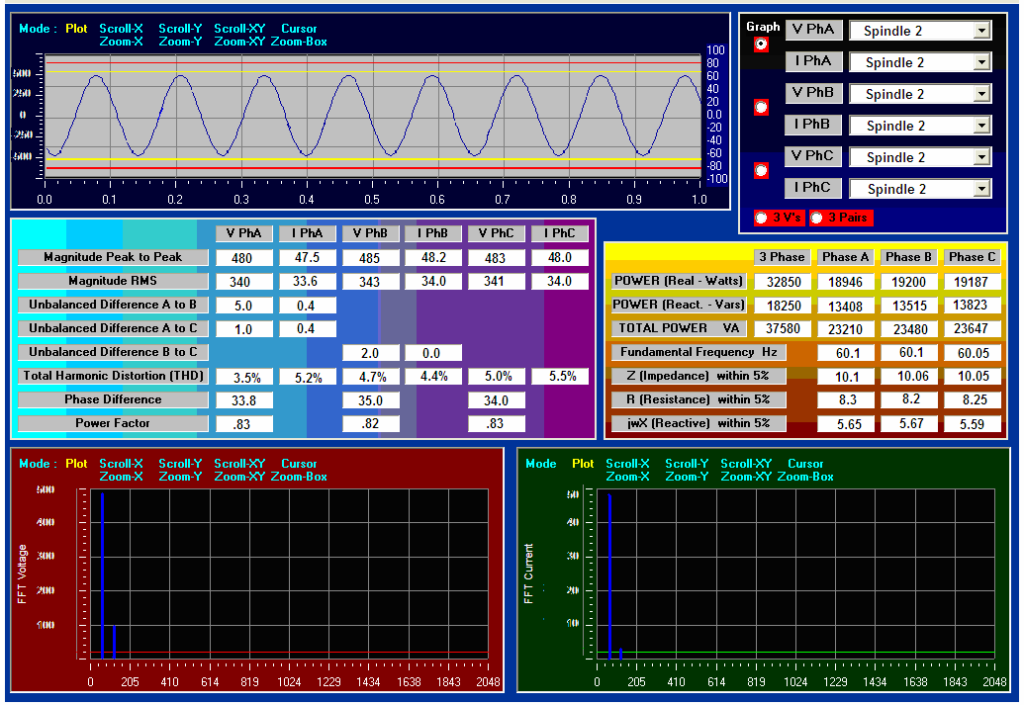
Figure No.19 MCA Analysis w/ Total Harmonic Distortion (THD), V&I balance, power factor,phase impendence values can be determined using temporary sensors connected toelectrical conductors or PT’s / CT’s.
Solution:tune VFD’s to provide uniform power to motors
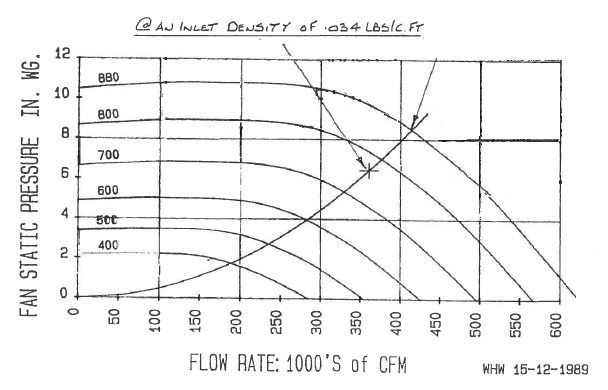
Figure No. 20 OEM Fan performance Data & Curves identify optimum machine loading
Solution: Understanding how the machines were designed to operate (OEM data) is a good analysis starting point.
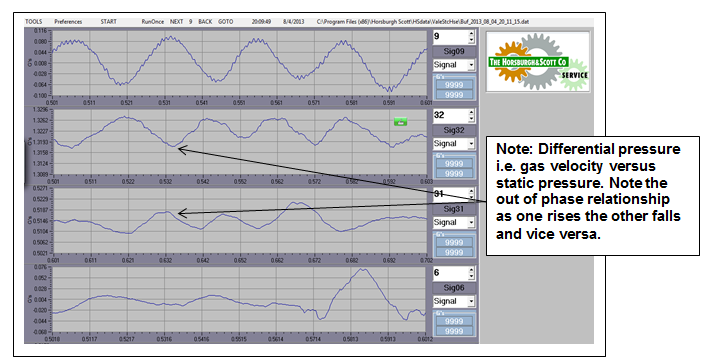
Figure No. 21 Multi-Channel transient event Trending and Analysis compares gas velocity, static pressure, with vibration.
Solution:High vibration w/ reliability issues can frequently be traced to process disturbances.
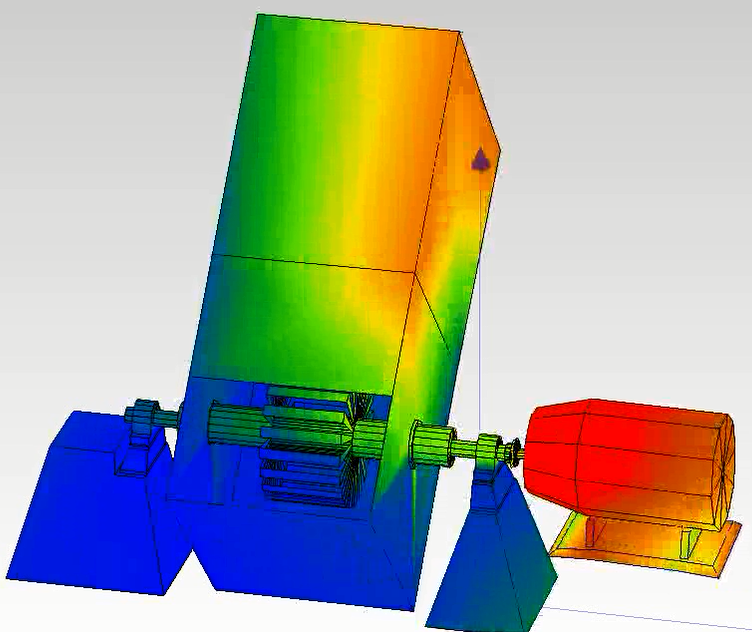
Figure No. 22 ODS Model of Fan illustration of how Gas flow disturbances effects motor vibration levels and motor reliability.
Solution: Repair discharge damper servo, clean ducts to discharge header and replace IB pillow block bearing
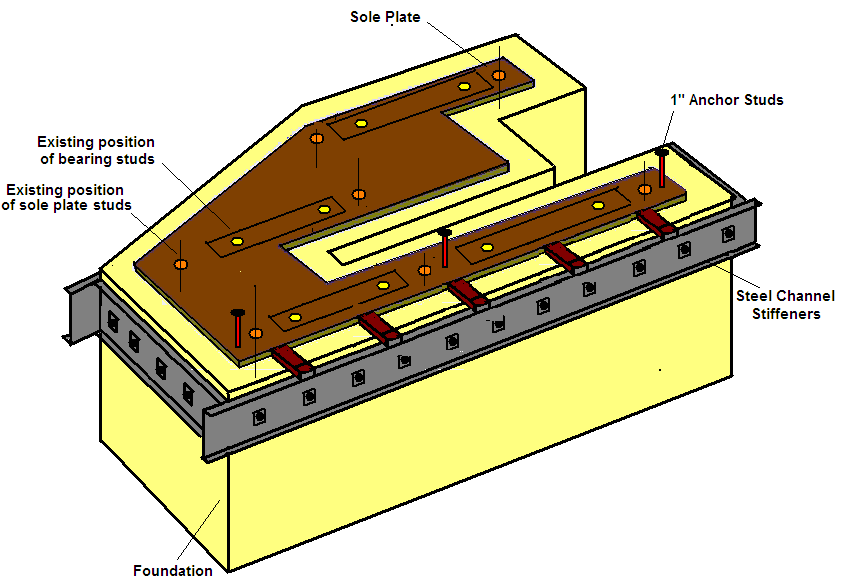
Figure No.23 Foundation / Sole Plate Repair Design to meet time window
Banking on our 20 years of experience, we can rightfully say that our vibration analysis procedures are the best in the market. Instead of offering basic “analyze and fix” services, we’re taking a few steps ahead. We understand that all machinery are destined to malfunction at one point or another, so we often adopt advanced condition monitoring strategies. We’re also aware of technology’s importance for every processing plant. As part of our consultancy framework, we also emphasize the need for advanced technology.
Many of our clients in the past were already at their wit’s end when they approached us. Their machinery and infrastructure problems have already run deep, causing exponential troubles. Here at Stan Engineering & Analysis, we take each client’s problem in a unique scaffold. Even though vibration condition analysis is our flagship service, we didn’t stop there. We usually include logical methods and predictive planning to solve all our clients’ troubles. Some of our best clients are heavy industrial firms, chemical processing plants, refineries, and steel processors. We also offer in-depth vibration analysis for modeling companies.
As part of our growing services, we’re also offering phone consultations for all of our clients. In every phone consultation, we’ll take all angles of the problem objectively. This will help us come up of a possible solution to the client’s problems.
Our service scope is currently North America, but we;re receiving inquiries from many locations outside the US. In light of this, we’ll probably consider expanding our service scope to take in more clients.
Do you have a growing machinery framework trouble within your company? Contact us today and we’ll talk about possible solutions!